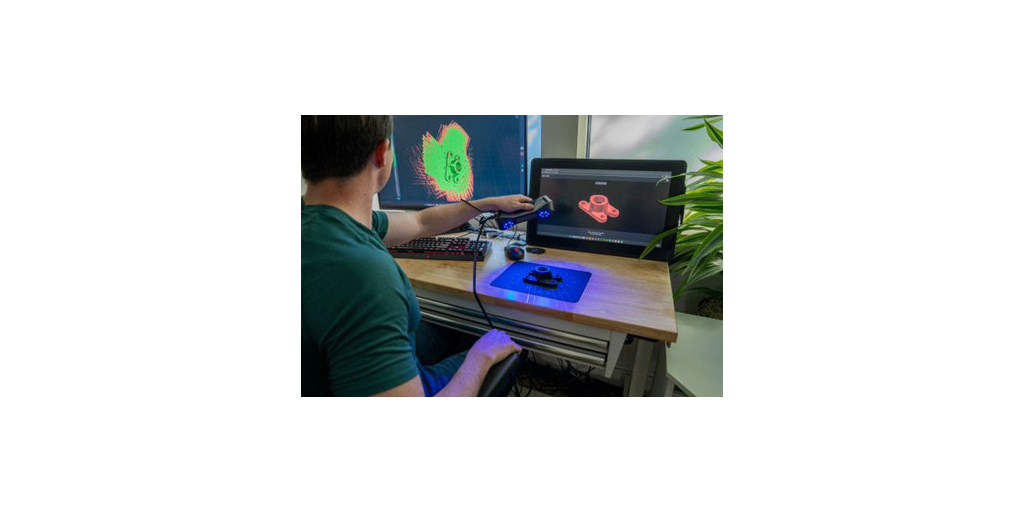
SAN FRANCISCO, CA, Mar 10, 2025 – Backflip AI unveiled a new 3D AI foundation model that primarily accelerates manufacturing plants’ repair and improvement to prevent costly downtime. The new technology allows anyone to automatically generate 3D models of replacement parts from 3D scan data. The models can be manufactured using traditional methods like CNC machining or 3D printing.
The company also announced two new AI-powered tools: A plug-in for SOLIDWORKS that translates 3D scan data into fully-featured parts in SOLIDWORKS’ native file format and a web app that converts 3D scans into parametric CAD files. Both tools simplify a process that used to be complex and expensive, thus reducing time.
Today, when a part unexpectedly breaks in a manufacturing plant, it can halt production and require immediate attention from the maintenance team. Since assembly lines consist of thousands of unique parts, keeping every spare part in stock is not feasible. Traditionally, maintenance teams must:
- Manually measure the part and create a digital 3D CAD model
- Manufacture a replacement at an internal or external machine shop
- Install the new part and restart production
Each of the above steps can take several hours, and research has shown that industrial manufacturers suffer over $50 billion in losses per year due to unexpected downtime. Backflip’s new tools eliminate the bottleneck in this process by instantly generating precise digital models, cutting repair time in half, and getting production lines back up and running faster.
A $3 million per hour problem
Automotive manufacturing is a complex, synchronized ballet of tens of thousands of parts, robots, machines, and people that come together in an interesting operation of automated assembly. If even one part breaks, an entire production line goes down at costs that can exceed $3 million per hour in lost output. Backflip’s new technology helps manufacturing teams compress the time from broken parts to digital 3D models, which helps get production back online faster.
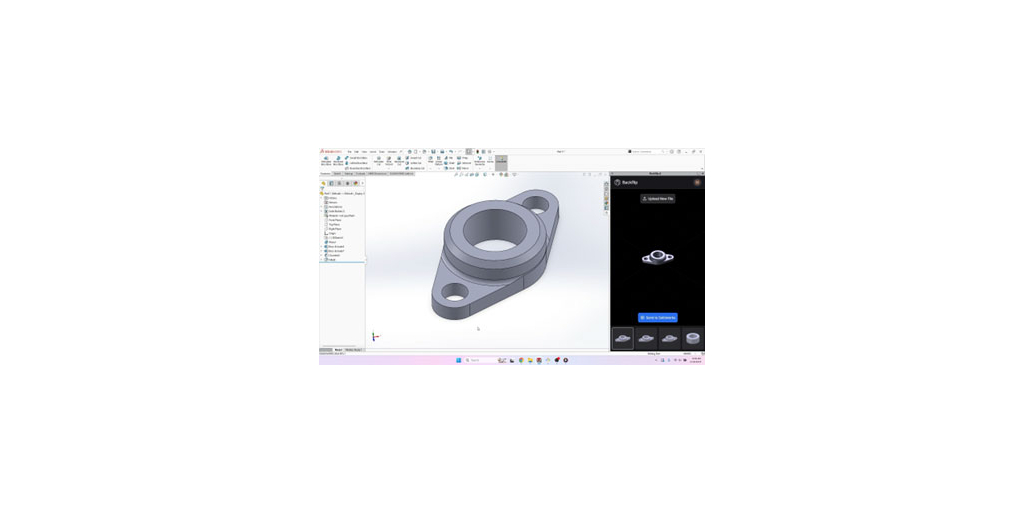
Beyond automotive, factory maintenance challenges exist across the $44 trillion global manufacturing sector. Many production lines are built by third-party system integrators who do not provide CAD models to their clients. Some components are no longer manufactured, and specific factory machines are older than digital design, particularly in aerospace. Consequently, manufacturing teams spend many hours each year recreating 3D models for parts they already possess. Backflip’s new tools resolve this issue by automatically converting 3D scans of these parts into CAD files suitable for manufacturing in around one minute.
Opening the door to 3D
Backflip’s developments reduce the technical barriers to entry for designers, engineers, and technicians to recreate 3D models of parts for which they don’t have CAD files. The tools simplify the process of 3D scanning, eliminating a long-standing challenge associated with the technology and its users.
“3D scanners map the surface of an object with incredible precision, quickly generating millions of data points, but they produce micro surface textures that can’t be manufactured with traditional tools. Our technology automatically converts these intricate surfaces into clean geometries designed for existing 3D CAD and manufacturing software,” noted Greg Mark, Backflip CEO and cofounder.
Teaching 3D design to new users
Backflip’s SOLIDWORKS plug-in shows each step in the process used to build a part’s geometry and generates a native feature history that users can modify. This enables CAD designers to fine- tune the generated 3D model. For new users, walking through the design process helps them understand how the part was created, flattening the learning curve for designing in 3D and bringing more people into 3D CAD programs like SOLIDWORKS.
Building AI for manufacturing
The new AI model was trained on Backflip’s synthetic 3D data set of over 100 million unique 3D geometries – – which continues to grow at an accelerating pace. Backflip head of AI Logan Ford added, “These new developments are the result of Backflip’s continued R&D investments in neural representation of 3D data. We’ve paired state-of-the-art AI/ML techniques with the team’s deep background in manufacturing to create a really powerful technology foundation. Our additional focus on resource-efficiency enables us to advance rapidly, and yields 60x more efficient training, 10x faster inference and 100x the spatial resolution of existing leading methods.”
Source: Backflip
About Backflip AI
Backflip AI, established in 2020, specializes in AI-powered 3D design tools that enable designers and engineers to transform their ideas into detailed models suitable for 3D printing or integration into digital platforms like video games and 3D renders. Its flagship products include ‘Scan-to-CAD’, which converts 3D scans into parametric CAD models, and ‘Idea-to-Mesh’, allowing users to generate 3D models from descriptions, sketches, or images. These innovations cater to industries such as automotive, architecture, gaming, film, and the metaverse. Backflip AI is headquartered in Miami, Florida, and has secured $30 million in funding over two rounds, with investors including Andreessen Horowitz and New Enterprise Associates.