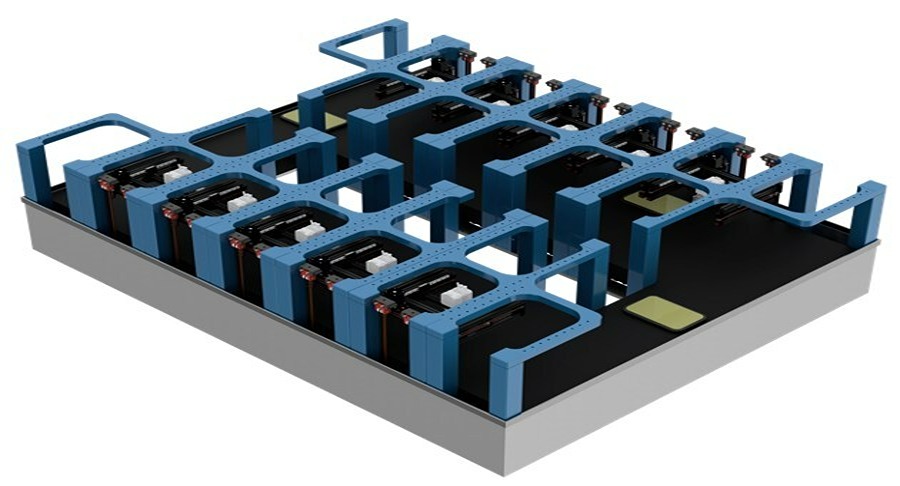
DETROIT, MI, Apr 9, 2025 – Advanced Printed Electronic Solutions (APES) has announced the launch of Matrix6D, a flexible, modular, adaptive additive manufacturing (AM) platform designed to address a key challenge in 3D printing: scalable production beyond the prototyping phase.
Matrix6D introduces a reconfigurable “swarm-based” approach to 3D printing that moves away from fixed-build platforms. Instead, it deploys mobile, magnetically levitated build units the company calls “mobile build platforms,” each orchestrated by software across configurable tool stations. The innovation enables parallelization, workflow flexibility, tool options, and throughput in additive production.
“Every customer we’ve worked with asks the same question: how do we scale 3D printing beyond prototyping? 6D is our answer,” said Rich Neill, CEO of APES. “It’s a clean-sheet reimagining of the additive factory – adaptive, software-defined, and built for mass customization and true production volume.”
An Adaptive Additive Manufacturing Architecture
At the heart of Matrix6D is a grid-based, XY-configurable tool-cell architecture that allows an arbitrary number of tool stations to be arranged in a matrix topology. Each station has different motion gantry options, which can be configured depending on the build volume and precision required. Every cell is a mini manufacturing unit equipped with any combination of material deposition—including aerosol jet, inkjet, direct write, dispensing, or extrusion—and non-additive processes. These include curing/post-processing, pick-and-place robots, or other tools, such as vision systems for calibration and inspection. Mobile build platforms autonomously move from station to station via magnetic levitation, enabling complex, multi-step manufacturing processes without the spatial and functional constraints of traditional 3D printers.
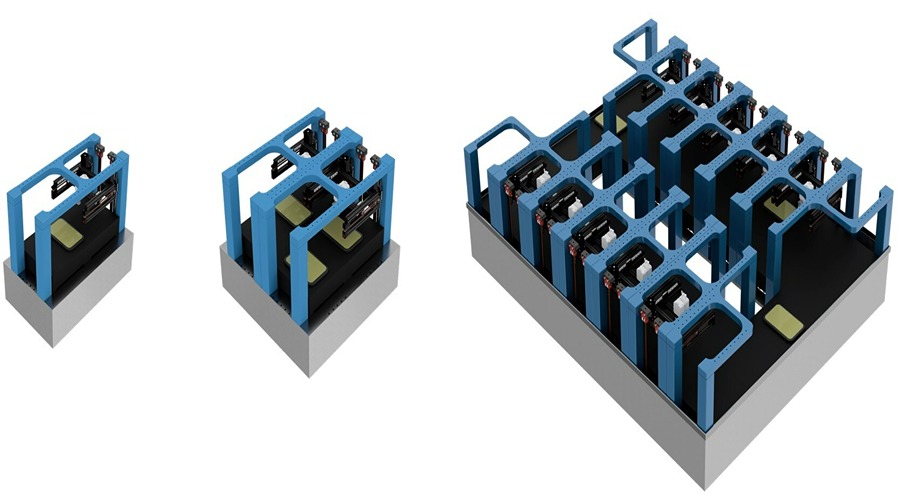
The platform supports mass customization, concurrent production of different parts, and dynamic task allocation via orchestration software. Each tool station utilizes machine vision or laser optics for self-calibration, ensuring micron-level precision even at scale. Matrix6D’s architecture supports multiple classes of accuracy—from standard industrial-grade builds to high-resolution requirements needed for semiconductor packaging and advanced nano-fabrication capabilities.
Scalability, Configurability, and Speed
The Matrix6D system scales from small benchtop setups to large-scale production lines. It supports different toolhead sizes, tool station densities, and build volumes, all defined parametrically. Multiple manufacturing recipes can handle multiple production recipes simultaneously, making them suitable for semiconductor and electronic packaging, additive manufacturing of circuit boards, and metamaterial optics.
Matrix6D will debut in person at RAPID + TCT 2025, where APES will showcase a working 1×2 demonstrator unit featuring a live extruder plus robotic handoff and dynamic mobile build platforms.
A Platform for the Future
Initially developed for additive electronics, Matrix6D is applied broadly. Its architecture supports various polymer-based processes and industrial automation. It is adapted to integrate emerging technologies, including volumetric additive manufacturing.
Source: Advanced Printed Electronic Solutions
About Advanced Printed Electronic Solutions (APES)
Advanced Printed Electronic Solutions (APES), founded in 2019 and headquartered in Fishkill, NY, specializes in multi-material, multi-tool, 5-axis additive manufactured electronics (AME). The company offers engineering services encompassing hardware and software development, process engineering, and manufacturing. APES serves aerospace, defense, medical devices, and consumer electronics industries, providing solutions for complex electronic systems. The company has formed strategic partnerships with organizations like KRONOS Mechatronics and Neotech AMT to enhance its offerings in 3D-printed electronics.