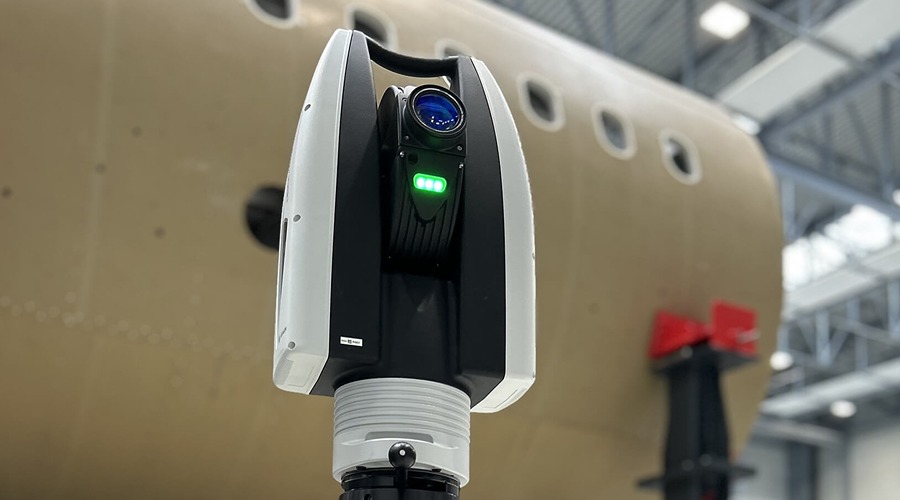
STUTTGART, Germany, May 9, 2025 – Amid increasing production demands and workforce challenges, Hexagon’s Manufacturing Intelligence division has launched the Leica Absolute Tracker ATS800. The system is intended for use in large-scale manufacturing environments, including aerospace and wind energy sectors. It enables direct scanning comparable to reflector-based systems. Its compact and lightweight design supports flexible deployment across various inspection scenarios.
Integrated into digital and robotic automation workflows, the ATS800 is designed to reduce inspection time and support real-time measurement and process alignment. It includes a feature recognition function, FeatureDetect, which identifies part geometries without manual programming. This capability reduces operator input and improves efficiency in both automated and manual quality inspections.
FeatureDetect operates from CAD data or independently, using the ATS800’s panoramic camera. The live image feed allows the system to recognize features from the physical part, accelerating set-up and streamlining inspection.
Designed for industries requiring inspection of large and complex structures, the ATS800 combines direct scanning and reflector tracking in one compact system. It shortens setup times and supports unattended or in-process inspection tasks – such as fuselage alignment and composite layup – while maintaining measurement accuracy and traceability.
“Today’s manufacturers are under immense pressure to increase output while maintaining the highest quality standards, and traditional labor-intensive processes can’t keep pace,” said Rodrigo Alfaia, laser tracker product director at Hexagon. “The ATS800 eliminates hours of setup and ‘boots-on-the-ground’ measurement activity without sacrificing precision. We’re physically and digitally automating large-scale inspection by bringing data-driven processes to the operational level, whether scanning a full fuselage overnight or guiding critical assembly processes in real time without the need for complex operator training.”
Digitally automated high-accuracy scanning
The ATS800 brings together Hexagon’s laser tracker capabilities with direct scanning in one compact unit. What’s notable is that it can perform measurements without a reflector at distances up to 40 meters. That makes it useful for inspecting large parts where getting close isn’t always possible. It can pick up features like edges, holes, slots, and threads without needing to make physical contact. On top of that, the built-in 3D reflector tracking helps speed up alignment and setup, particularly useful for large-structure inspections and assemblies.
FeatureDetect uses AI to identify measurement features from CAD models or panoramic views, reducing the need for manual programming. It simplifies large-structure inspection workflows and supports flexible, semi-autonomous operation with less dependence on experienced personnel.
Compatible with metrology software platforms like PC-DMIS, SpatialAnalyzer and third-party alternatives, the system works with existing setups and Hexagon’s automation software, supporting a gradual move to high-throughput inspection with minimal workflow changes.
Robotic and AGV/AMR automation
The ATS800 is designed for portability and flexible deployment. Its compact size allows mounting in various orientations, including upside down. It can be integrated with AMRs, gantries, lifts, rails, or robot arms, making it suitable for space-constrained or high-traffic shop floors while supporting safe and efficient inspection workflows.
The ATS800 comes with a full SDK, which makes it easier to integrate into advanced robotic setups. That means it can handle tasks like automated feature measurement, real-time part tracking, and process control. It works whether it’s mounted on a fixed lift-and-rail system or moving around on an AMR. Either way, It offers engineers a flexible option for unattended or continuous inspections.
For example, the ATS800 will be powering Hexagon’s PRESTO Quality Stations, where it is combined with high-speed 2 axis positioning to automate the inspection of automotive chassis features. With long-range, reflectorless scanning, it’s possible to inspect several complex features using a single axis of motion – either vertically or horizontally. That simplifies the movement needed and helps bring down cycle times while improving consistency and throughput.
Unlocking “third-shift” workflows and real-time assembly
As manufacturing industries scale up, the need for in-process or overnight inspection is increasing. The ATS800 supports this with unattended scanning, real-time tracking, and subassembly alignment. It enables tasks like fuselage integration or composite layup inspection to be performed without halting production, while maintaining precision and providing digital traceability.
At the heart of the system is Hexagon’s TruePoint Interferometer, a next-generation measurement engine that minimizes noise and delivers pinpoint accuracy, even on challenging surfaces or at steep angles.
When mobility is required, Hexagon’s proprietary PowerLock reacquisition technology re-locks onto reflectors in motion, ensuring continuous measurement during real-time assembly.
About Hexagon
Hexagon AB, established in 1975, specializes in digital reality solutions integrating sensors, software, and autonomous technologies. Headquartered in Stockholm, Sweden, Hexagon operates in over 50 countries and employs approximately 24,800 people. The company serves a diverse range of industries, including construction, mining, agriculture, aerospace, automotive, defense, and manufacturing. Its offerings encompass reality capture measurement, intelligent positioning, situational intelligence, and industrial design solutions. In 2023, Hexagon reported annual revenues of approximately €5.44 billion. Since 2000, Hexagon has completed over 170 strategic acquisitions, enhancing its position in digital transformation and enabling clients to utilize data for improved efficiency, productivity, quality, and safety across various applications.