BURNTWOOD, UK, Feb 25, 2025 – Lesters has customers across automotive, engineering, medical and retail tapping into the company’s ecosystem that takes them from the core box range and specialist design through to supply chain services and an enhanced innovation and R&D offer.
Utilization of two state-of-the-art TCY large format casemakers has transformed production speeds and capacity at its 60,000 sq ft facility on Mount Road and this has been supplemented by the recruitment of eight new people across sales, design and manufacturing.
The latest hire is Edward Scobie, joining the company as the operations manager. He will provide a pivotal link between production and the general manager, with the remit to drive productivity improvements, maintain top quality standards and unlock more capacity by leveraging real time data.
Billy Hutchinson, managing director of Lesters, commented: “There were lots of challenges in 2024, many of them outside our control and driven by external pressures.”
“Despite the volatile outlook, we’ve continued to expand and are confident that we’ll hit £25m by the end of the next financial year – a successful completion of our four-year growth plan.” He continued: “A big part of this has been our fantastic Lesters team, who go above and beyond to ensure our customers receive timely packaging solutions that meet their exact requirements.”
“We’ve also looked at how we can create a complete ecosystem for our clients, which means they have access to design support and core packaging, right through to supply chain solutions and stock management through Lesters Logistics.”
Another key development for the business has been Greg Burton’s transition from design manager to design innovation lead. This is a natural transition and will see him strengthen his role as the conduit between the sales team and customers by spending more time on the road visiting clients’ warehouses and facilities. It is anticipated that this new position will give him more opportunity to explore supply chains, getting to know how they operate and what they need in terms of packaging and how design innovation could reduce their costs.
Billy went on to add: “You can’t stand still in our industry and that is why we’re always looking to innovate and attempting to do things differently.”
“2025 will be no different. One really exciting development will be working towards the BRCGS Global Food Safety Standard mark. This provides a framework to manage product safety, integrity, legality, quality and operational controls for food and food ingredient manufacturing.”
“It’s a lengthy process to achieve the mark, and our efforts, led by Project Manager Cerianne Dixon and Business Support Manager Richard Shorthouse, are still ongoing. However, we’re confident that by the summer we’ll have achieved the Standard, opening up new markets for us in the process.”
About Lesters Packaging
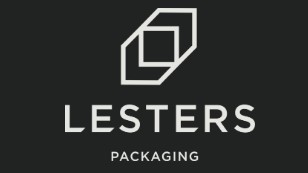
Lesters Packaging, established in 1983, specializes in designing and producing heavy-duty corrugated cardboard packaging solutions. The company serves a diverse range of industries, including retail, industrial, electronics, aerospace, automotive parts, logistics and fulfillment, and the grower’s market. Their product offerings include octabin boxes, pick bins, bike boxes, pallet boxes, die-cut boxes, removal boxes, corrugated cartons, shuttle packs, heavy-duty packaging, retail-ready packaging, and extra-large cardboard boxes. Headquartered in the West Midlands, UK, Lesters Packaging operates state-of-the-art manufacturing facilities, providing bespoke packaging solutions to businesses of all sizes. While specific annual revenue figures are not publicly disclosed, the company’s longstanding presence and extensive industry expertise underscore its commitment to delivering high-quality, customized packaging solutions.