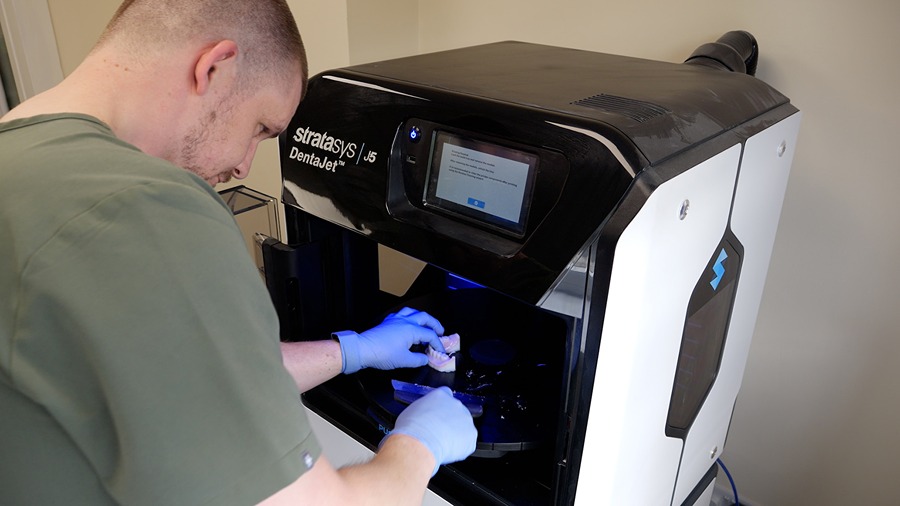
DERBY, UK, July 14, 2025 – SYS Systems has reported a 350% increase in dental market sales, driven by the adoption of Stratasys J5 DentaJet 3D printers in UK clinics and laboratories. These systems produce removable dentures that offer both aesthetics and function, while reducing production time by around 50%. The trend reflects the integration of additive manufacturing into clinical systems.
The J5 DentaJet uses a patented, CE-marked resin, TrueDent. The resin is recognized for its durability and its ability to print multiple tooth and base shades simultaneously within a single, full-color, monolithic structure.
Matt Fulton, managing director at SYS Systems, commented, “Additive manufacturing is revolutionizing the way we make things, and the dental market is the latest to switch on to the benefits. It’s a real win-win for dentists and labs. The 3D printed prosthetics are versatile, highly durable and deliver the best aesthetics – all achieved in half the time it takes compared to the traditional route.”
He added, “Stratasys’ J5 DentaJet is the most advanced printer in this space and, when you combine it with the TrueDent resin, it’s not a surprise that demand is soaring in the UK and Ireland. In fact, I think we’re leading the way when it comes to sales of this machine in Europe.”
According to SYS Systems, a new J5 DentaJet is being installed every two weeks. The uptake is attributed to the printer’s speed, functionality, and aesthetics. Dental laboratories benefit from the flexibility to produce solutions ranging from monolithic dentures and temporaries to crown and bridge models.
Prime Dental Laboratory in Ilkeston has been one of the first in Europe to use both the J5 DentaJet and TrueDent resin. In partnership with SYS Systems, Prime Dental has used the technology to improve both clinical results and productivity.
Tim Jackson, Prime Dental’s co-owner and clinical dental technician, explained the change: “From the start of my career, I worked completely analogue, and I would set everything up by hand. In more recent years, we have invested heavily into the digital side of dentistry and have seen a big change with dentists wanting to use it as well.”
He continued, “Digital dentures have sometimes been a little brittle in the past – not this TrueDent material, which I believe is the best printer resin on the market, surpassing everything I could have imagined strength-wise, as well as aesthetics. For example, we’ve thrown it down the corridor and even stomped on it and it’s unbreakable.”
“Speed has also been important. Creating using an analogue method, we found that 18 dentures would take us around 12 hours to make. Doing the same process digitally, we went down to about six hours, and – now we’ve got the J5 DentaJet – we can knock another hour off that just on post-processing those dentures as well.”
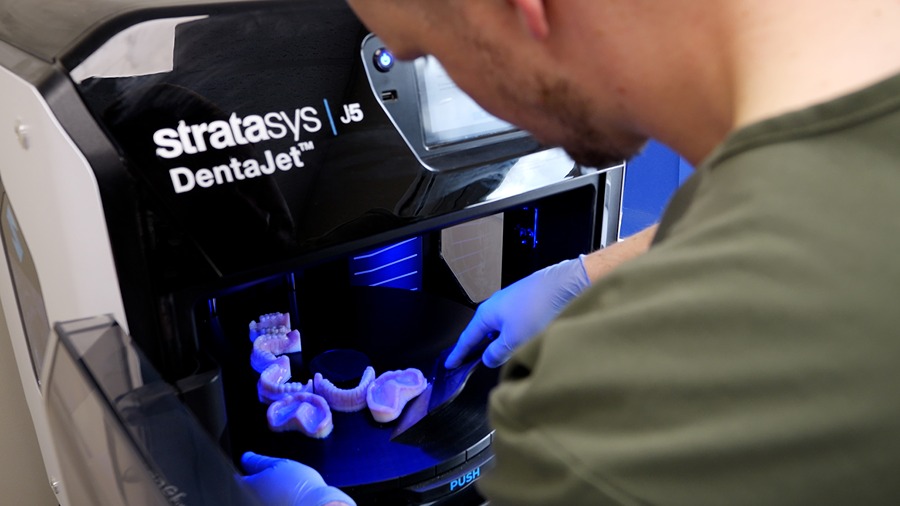
Zenith Dental Clinic in Nottingham is collaborating with Prime Dental. Principal dentist Dr. Karan Maini described his initial skepticism toward digital methods and subsequent change in approach: “I had many reservations about digital dentistry in general. I was very much of the mindset that I wanted to do everything traditionally. I didn’t even use a scanner at all. After I tried a scanner for the first time, I thought that’s quite good. Then you try another time, and it starts to get really interesting. Before you know it, I’ve been introduced to TrueDent and Stratasys through SYS Systems and here we are. Every denture I make is now a TrueDent denture.”
Dr. Maini added, “Digital adoption has had a big impact on our clients and our patients, with reduced chair time and patients being able to get their desired end result within a matter of days rather than weeks.”
Source: SYS Systems
About SYS Systems
SYS Systems is a UK-based provider of additive manufacturing solutions and the country’s official platinum partner for Stratasys, a manufacturer of 3D printing technologies. Established in 2007 and operating from the Advanced Innovation Centre in Foston, Derby, SYS Systems supplies and supports the range of Stratasys 3D printing platforms, including FDM, PolyJet, SAF, and P3 systems. Their offering includes not only hardware and materials but also installation, maintenance, training, and technical support. The company serves a range of industries across the UK and Ireland, including aerospace, automotive, medical, dental, rail, defense, consumer goods, education, and research. SYS Systems works with manufacturers and institutions to integrate 3D printing into production and prototyping workflows. It is a division of the Carfulan Group, which focuses on delivering manufacturing technologies. SYS Systems also contributes to the parent group’s efforts in supporting digital transformation in manufacturing environments.
About Carfulan Group
Carfulan Group, founded in 1989 and headquartered at its Advanced Innovation Centre in Foston, Derbyshire, is a privately owned engineering company focused on delivering precision manufacturing technologies. Managed by brothers Chris and Matt Fulton, the group operates through five divisions: OGP UK (multi-sensor inspection), SYS Systems (additive manufacturing), ZOLLER UK (tool presetting and measurement), VICIVISION UK (turned-part measurement), and Prolink UK (SPC and data software). These technologies serve production and quality assurance needs across sectors such as aerospace, automotive, medical, defense, rail, oil and gas, consumer goods, and education. The company supports over 700 clients across the UK and Ireland, offering installation, training, and technical support. Carfulan employs more than 60 staff and reported over £10 million in revenue in 2025, with a stated goal of reaching £40 million by 2030. Its operations focus on improving dimensional accuracy, production control, and digital integration within manufacturing workflows.